نه، راستش را بخواهید، این خستهکننده نخواهد بود - مخصوصاً اگر عاشق چیزهای لاستیکی کشسان باشید. اگر ادامه مطلب را بخوانید، تقریباً هر چیزی را که میخواستید در مورد درزگیرهای سیلیکونی تک جزئی بدانید، خواهید فهمید.
۱) چیستی آنها
۲) نحوه ساخت آنها
۳) کجا از آنها استفاده کنیم
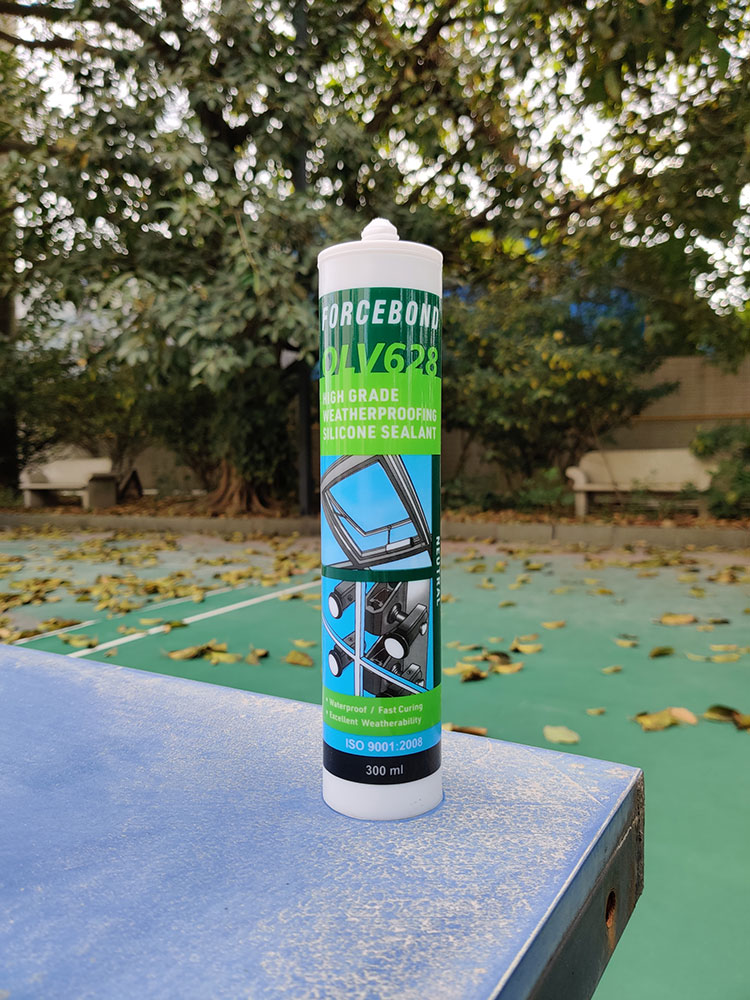
مقدمه
درزگیر سیلیکونی تک جزئی چیست؟
انواع مختلفی از درزگیرهای شیمیایی وجود دارد که سیلیکون، پلی اورتان و پلی سولفید شناخته شده ترین آنها هستند. نام آنها از ساختار مولکول های تشکیل دهنده آنها گرفته شده است.
اسکلت سیلیکونی:
Si – O – Si – O – Si – O – Si
سیلیکون اصلاحشده یک فناوری جدید است (حداقل در ایالات متحده) و در واقع به معنای یک اسکلت آلی است که با شیمی سیلان پخت میشود. به عنوان مثال میتوان به پلیپروپیلن اکسید با انتهای آلکوکسیسیلان اشاره کرد.
تمام این ترکیبات شیمیایی میتوانند تک جزئی یا دو جزئی باشند که بدیهی است به تعداد اجزایی که برای پخت نیاز دارید، مربوط میشود. بنابراین، یک جزئی به سادگی به معنای باز کردن لوله، کارتریج یا سطل است و ماده شما پخت خواهد شد. به طور معمول، این سیستمهای تک جزئی با رطوبت موجود در هوا واکنش نشان میدهند و به لاستیک تبدیل میشوند.
بنابراین، سیلیکون تک جزئی سیستمی است که در لوله پایدار میماند تا زمانی که در معرض هوا قرار گیرد و تبدیل به لاستیک سیلیکونی شود.
مزایا
سیلیکونهای تک جزئی مزایای منحصر به فرد زیادی دارند.
-وقتی به درستی ترکیب شوند، بسیار پایدار و قابل اعتماد با چسبندگی و خواص فیزیکی عالی هستند. ماندگاری (مدت زمانی که میتوانید قبل از استفاده آن را در تیوب بگذارید) حداقل یک سال طبیعی است و برخی از فرمولاسیونها برای سالهای زیادی دوام میآورند. سیلیکونها همچنین بدون شک بهترین عملکرد بلندمدت را دارند. خواص فیزیکی آنها به مرور زمان به سختی تغییر میکند و هیچ تاثیری از قرار گرفتن در معرض اشعه ماوراء بنفش ندارند و علاوه بر این، پایداری دمایی عالی را نشان میدهند که حداقل 50 درجه سانتیگراد از سایر درزگیرها بیشتر است.
سیلیکونهای تک جزئی نسبتاً سریع خشک میشوند، معمولاً ظرف ۵ تا ۱۰ دقیقه پوسته تشکیل میدهند، ظرف یک ساعت چسبندگی خود را از دست میدهند و در کمتر از یک روز به یک لاستیک الاستیک با عمق حدود ۱/۱۰ اینچ تبدیل میشوند. سطح آن حس لاستیکی خوبی دارد.
-از آنجایی که میتوان آنها را شفاف ساخت که خود یک ویژگی مهم است (شفاف پرکاربردترین رنگ است)، رنگآمیزی آنها به هر رنگی نسبتاً آسان است.
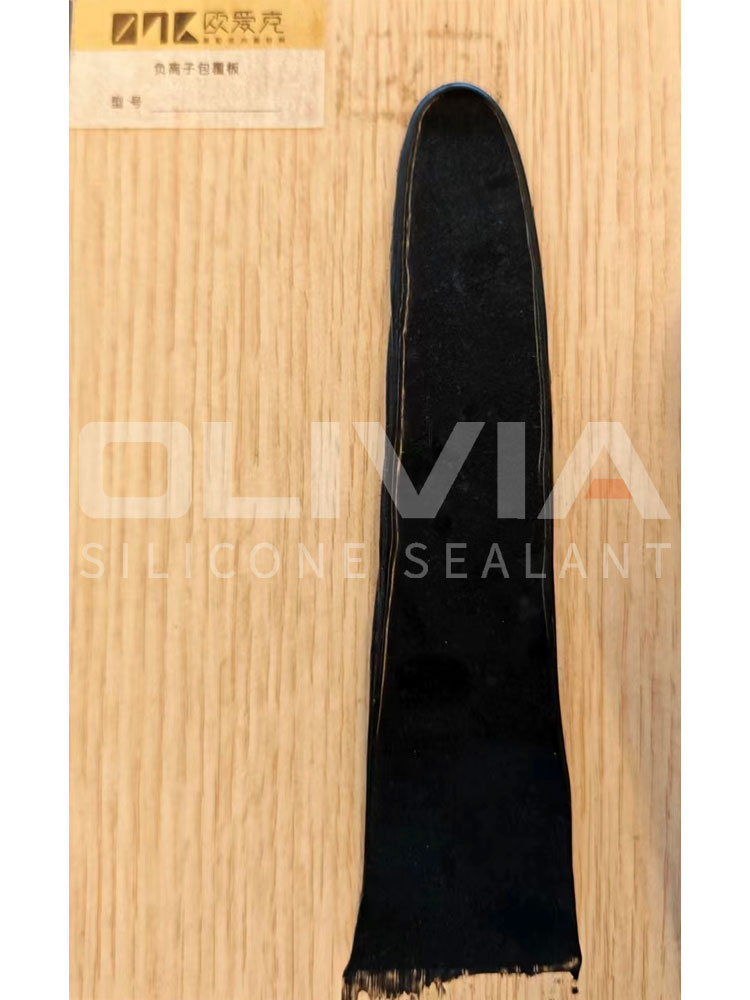
محدودیتها
سیلیکونها دو محدودیت اصلی دارند.
۱) آنها را نمیتوان با رنگ پایه آب رنگ کرد - همچنین با رنگ پایه حلال میتواند مشکل باشد.
۲) پس از خشک شدن، درزگیر میتواند مقداری از نرمکننده سیلیکونی خود را آزاد کند که هنگام استفاده در درز انبساط ساختمان، میتواند لکههای نازیبایی در امتداد لبه درز ایجاد کند.
البته، به دلیل ماهیت تک جزئی بودن، رسیدن به یک مقطع عمیق سریع از طریق پخت غیرممکن است زیرا سیستم باید با هوا واکنش نشان دهد و بنابراین از بالا به پایین پخت شود. اگر کمی دقیقتر شویم، سیلیکونها را نمیتوان به عنوان تنها درزگیر در پنجرههای شیشهای عایق استفاده کرد زیرا اگرچه آنها در جلوگیری از ورود آب مایع به صورت فلهای عالی هستند، اما بخار آب به راحتی از لاستیک سیلیکونی پخت شده عبور میکند و باعث مه گرفتگی واحدهای IG میشود.
مناطق بازار و موارد استفاده
سیلیکونهای تک جزئی تقریباً در هر جایی و در هر مکانی استفاده میشوند، از جمله، با وجود نگرانی برخی از صاحبان ساختمان، که در آنها دو محدودیت ذکر شده در بالا باعث ایجاد مشکل میشود.
بازارهای ساخت و ساز و DIY حجم عمدهای از بازار را به خود اختصاص میدهند و پس از آن بازارهای خودرو، صنعت، الکترونیک و هوافضا قرار دارند. همانند تمام درزگیرها، عملکرد اصلی سیلیکونهای تک جزئی، چسباندن و پر کردن شکاف بین دو زیرلایه مشابه یا غیر مشابه برای جلوگیری از عبور آب یا جریان هوا است. گاهی اوقات یک فرمولاسیون به سختی تغییر میکند، مگر اینکه روانتر شود و سپس به یک پوشش تبدیل شود. بهترین راه برای تمایز بین پوشش، چسب و درزگیر ساده است. درزگیر بین دو سطح آببندی میکند در حالی که یک پوشش فقط یک سطح را میپوشاند و محافظت میکند در حالی که یک چسب به طور گسترده دو سطح را در کنار هم نگه میدارد. درزگیر وقتی در لعاب سازهای یا لعاب عایق استفاده میشود، بیشتر شبیه چسب است، با این حال، علاوه بر نگه داشتن دو زیرلایه در کنار هم، وظیفه آببندی آنها را نیز بر عهده دارد.
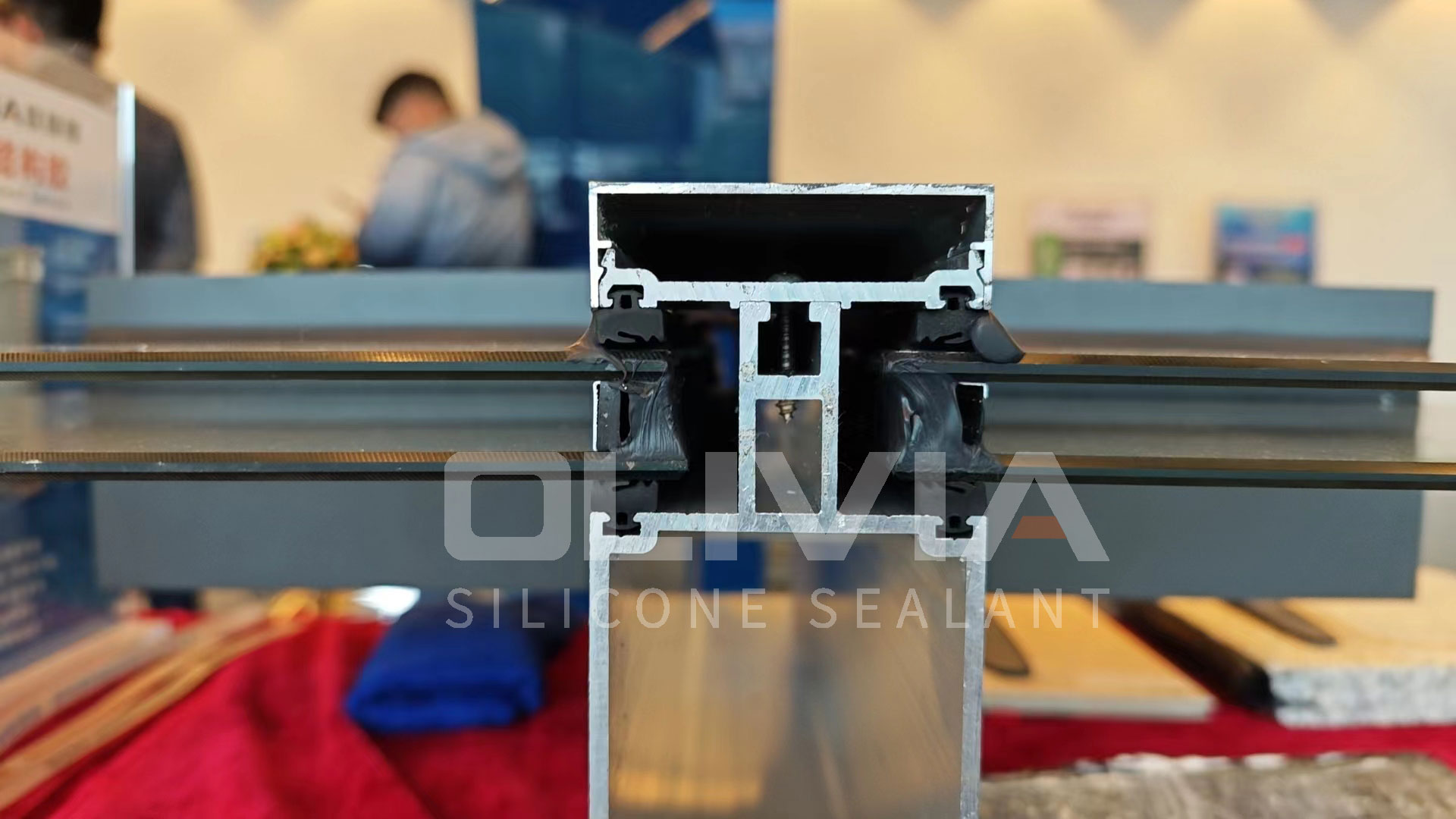
شیمی پایه
درزگیر سیلیکونی در حالت پخت نشده معمولاً شبیه یک خمیر یا کرم غلیظ است. در معرض هوا، گروههای انتهایی واکنشپذیر پلیمر سیلیکون هیدرولیز میشوند (با آب واکنش میدهند) و سپس به یکدیگر متصل میشوند، آب آزاد میکنند و زنجیرههای پلیمری بلندی تشکیل میدهند که به واکنش با یکدیگر ادامه میدهند تا در نهایت خمیر به یک لاستیک چشمگیر تبدیل شود. گروه واکنشپذیر در انتهای پلیمر سیلیکون از مهمترین بخش فرمولاسیون (به استثنای خود پلیمر) یعنی پیوند دهنده عرضی ناشی میشود. این پیوند دهنده عرضی است که به درزگیر خواص مشخصه خود را میدهد، چه به طور مستقیم مانند بو و سرعت پخت، و چه به طور غیرمستقیم مانند رنگ، چسبندگی و غیره، به دلیل سایر مواد اولیهای که ممکن است با سیستمهای پیوند دهنده عرضی خاص مانند پرکنندهها و تقویتکنندههای چسبندگی استفاده شوند. انتخاب پیوند دهنده عرضی مناسب، کلید تعیین خواص نهایی درزگیر است.
انواع عمل آوری
چندین سیستم پخت مختلف وجود دارد.
۱) استوکسی (بوی سرکه اسیدی)
۲) اکسیم
۳) آلکوکسی
۴) بنزامید
۵) آمین
۶) آمینوکسی
اکسیمها، آلکوکسیها و بنزامیدها (که بیشتر در اروپا مورد استفاده قرار میگیرند) سیستمهای خنثی یا غیراسیدی نامیده میشوند. سیستمهای آمین و آمینوکسی بوی آمونیاک دارند و معمولاً بیشتر در مناطق خودرو و صنعتی یا کاربردهای خاص ساخت و ساز در فضای باز استفاده میشوند.
مواد اولیه
فرمولاسیونها شامل چندین جزء مختلف هستند که برخی از آنها بسته به کاربرد نهایی مورد نظر، اختیاری هستند.
تنها مواد اولیه کاملاً ضروری، پلیمر واکنشپذیر و عامل اتصال عرضی هستند. با این حال، پرکنندهها، بهبوددهندههای چسبندگی، پلیمر غیر واکنشپذیر (نرمکننده) و کاتالیزورها تقریباً همیشه اضافه میشوند. علاوه بر این، میتوان از بسیاری از افزودنیهای دیگر مانند خمیرهای رنگی، قارچکشها، مواد ضد شعله و تثبیتکنندههای حرارتی استفاده کرد.
فرمولاسیونهای پایه
یک ساختار اکسیم معمولی یا فرمولاسیون درزگیر DIY چیزی شبیه به این خواهد بود:
% | ||
پلیدیمتیلسیلوکسان، OH با سرعت ۵۰۰۰۰ سیپییو خاتمه یافته | ۶۵.۹ | پلیمر |
پلیدیمتیلسیلوکسان، تریمتیلترمینات، ۱۰۰۰ سیپییو | 20 | پلاستیک ساز |
متیل تری اکسی مینوسیلان | 5 | کراس لینکر |
آمینوپروپیل تری اتوکسی سیلان | 1 | افزایش دهنده چسبندگی |
۱۵۰ متر مربع بر گرم سطح سیلیس دودی | 8 | پرکننده |
دیبوتیلتین دیلورات | ۰.۱ | کاتالیزور |
مجموع | ۱۰۰ |
خواص فیزیکی
خواص فیزیکی معمول عبارتند از:
کشیدگی (%) | ۵۵۰ |
استحکام کششی (مگاپاسکال) | ۱.۹ |
مدول در ۱۰۰ ازدیاد طول (مگاپاسکال) | ۰.۴ |
سختی ساحل A | 22 |
پوست در طول زمان (دقیقه) | 10 |
زمان آزاد تک (دقیقه) | 60 |
زمان خراش (دقیقه) | ۱۲۰ |
خشک شدن کامل (میلیمتر در ۲۴ ساعت) | 2 |
فرمولاسیونهایی که از سایر عوامل اتصال عرضی استفاده میکنند، ظاهری مشابه خواهند داشت، شاید تفاوت در سطح عامل اتصال عرضی، نوع بهبوددهنده چسبندگی و کاتالیزورهای پخت. خواص فیزیکی آنها کمی متفاوت خواهد بود مگر اینکه از افزایشدهندههای زنجیره استفاده شود. برخی از سیستمها را نمیتوان به راحتی ساخت، مگر اینکه از مقدار زیادی پرکننده گچی استفاده شود. بدیهی است که این نوع فرمولاسیونها را نمیتوان در نوع شفاف یا نیمهشفاف تولید کرد.
توسعه درزگیرها
سه مرحله برای توسعه یک درزگیر جدید وجود دارد.
۱) ایدهپردازی، تولید و آزمایش در آزمایشگاه - حجم بسیار کم
در اینجا، شیمیدان آزمایشگاه ایدههای جدیدی دارد و معمولاً با یک بسته دستی حدود ۱۰۰ گرمی از درزگیر شروع میکند تا ببیند چگونه عمل میآید و چه نوع لاستیکی تولید میشود. اکنون یک دستگاه جدید به نام "مخلوط سریع هاوچایلد" از شرکت FlackTek موجود است. این دستگاه تخصصی برای مخلوط کردن این بستههای کوچک ۱۰۰ گرمی در عرض چند ثانیه و با خارج کردن هوا ایدهآل است. این مهم است زیرا اکنون به توسعهدهنده اجازه میدهد تا خواص فیزیکی این بستههای کوچک را آزمایش کند. سیلیس بخار شده یا سایر پرکنندهها مانند گچهای رسوبی را میتوان در حدود ۸ ثانیه با سیلیکون مخلوط کرد. هواگیری حدود ۲۰ تا ۲۵ ثانیه طول میکشد. این دستگاه با استفاده از یک مکانیسم سانتریفیوژ نامتقارن دوگانه کار میکند که اساساً از خود ذرات به عنوان بازوهای مخلوطکننده خود استفاده میکند. حداکثر اندازه مخلوط ۱۰۰ گرم است و انواع مختلف فنجان از جمله یکبار مصرف موجود است، به این معنی که مطلقاً نیازی به تمیز کردن ندارد.
نکته کلیدی در فرآیند فرمولاسیون نه تنها نوع مواد تشکیل دهنده، بلکه ترتیب افزودن و زمان اختلاط نیز میباشد. طبیعتاً حذف یا عدم ورود هوا برای افزایش ماندگاری محصول مهم است، زیرا حبابهای هوا حاوی رطوبت هستند که باعث میشود درزگیر از درون خشک شود.
وقتی شیمیدان نوع درزگیر مورد نیاز برای کاربرد خاص خود را تهیه کرد، میتواند از یک میکسر سیارهای ۱ لیتری استفاده کند که میتواند حدود ۳-۴ لوله کوچک ۱۱۰ میلیلیتری (۳ اونسی) تولید کند. این ماده برای آزمایش اولیه ماندگاری و آزمایش چسبندگی به علاوه سایر الزامات خاص کافی است.
سپس او ممکن است به یک دستگاه ۱ یا ۲ گالنی برود تا ۸ تا ۱۲ لوله ۱۰ اونسی برای آزمایشهای عمیقتر و نمونهگیری مشتری تولید کند. درزگیر از طریق یک استوانه فلزی از دیگ به داخل کارتریجی که روی استوانه بستهبندی قرار میگیرد، اکسترود میشود. پس از این آزمایشها، او آماده افزایش مقیاس است.
۲) افزایش مقیاس و تنظیم دقیق - حجمهای متوسط
در مقیاس بزرگتر، فرمولاسیون آزمایشگاهی اکنون روی دستگاه بزرگتری معمولاً در محدوده ۱۰۰ تا ۲۰۰ کیلوگرم یا حدود یک بشکه تولید میشود. این مرحله دو هدف اصلی دارد.
الف) بررسی اینکه آیا تغییرات قابل توجهی بین اندازه ۴ پوندی و این اندازه بزرگتر وجود دارد که میتواند ناشی از سرعت اختلاط و پراکندگی، سرعت واکنش و مقادیر مختلف ضخامت در مخلوط باشد، و
ب) تولید مواد کافی برای نمونهگیری از مشتریان بالقوه و دریافت بازخورد واقعی در حین کار.
این دستگاه ۵۰ گالنی همچنین برای محصولات صنعتی بسیار مفید است، زمانی که حجم کم یا رنگهای خاص مورد نیاز است و فقط حدود یک بشکه از هر نوع در یک زمان نیاز به تولید دارد.
انواع مختلفی از دستگاههای مخلوطکن وجود دارد. دو مورد از رایجترین آنها، مخلوطکنهای سیارهای (همانطور که در بالا نشان داده شده است) و پخشکنندههای پرسرعت هستند. مخلوطکن سیارهای برای مخلوطهای با ویسکوزیته بالاتر مناسب است، در حالی که مخلوطکنهای پخشکننده به ویژه در سیستمهای روان با ویسکوزیته پایینتر عملکرد بهتری دارند. در درزگیرهای ساختمانی معمولی، میتوان از هر دو دستگاه استفاده کرد، به شرطی که به زمان مخلوط کردن و تولید گرمای بالقوه یک مخلوطکن پرسرعت توجه شود.
۳) مقادیر تولید در مقیاس کامل
تولید نهایی، که ممکن است دستهای یا پیوسته باشد، به سادگی فرمول نهایی را از مرحله افزایش مقیاس بازتولید میکند. معمولاً مقدار نسبتاً کمی (۲ یا ۳ دسته یا ۱-۲ ساعت مداوم) از مواد ابتدا در تجهیزات تولید تولید میشود و قبل از شروع تولید عادی بررسی میشود.
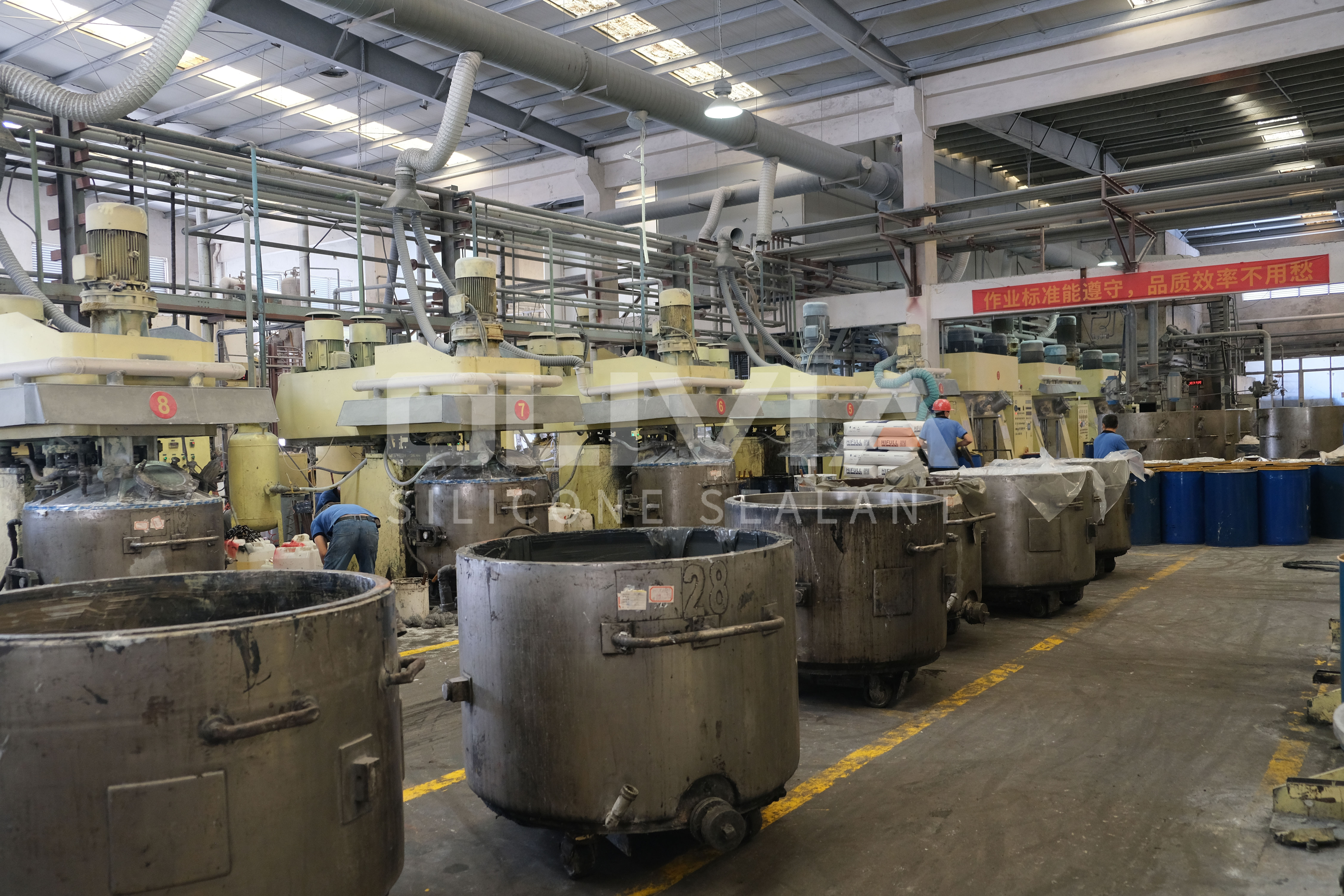
آزمایش - چه چیزی و چگونه آزمایش کنیم.
چه
خواص فیزیکی - ازدیاد طول، استحکام کششی و مدول
چسبندگی به زیرلایه مناسب
ماندگاری - هم در دمای اتاق و هم در دمای تسریع شده
نرخ خشک شدن - پوسته شدن به مرور زمان، زمان آزاد شدن چسب، زمان خراش و خشک شدن کامل، ثبات دما یا ثبات رنگ در مایعات مختلف مانند روغن
علاوه بر این، سایر خواص کلیدی بررسی یا مشاهده میشوند: قوام، بوی کم، خورندگی و ظاهر کلی.
چگونه
یک ورق درزگیر بیرون کشیده شده و به مدت یک هفته برای خشک شدن رها میشود. سپس یک دمبل مخصوص بریده شده و در دستگاه تست کشش قرار داده میشود تا خواص فیزیکی مانند ازدیاد طول، مدول و استحکام کششی اندازهگیری شود. همچنین از آنها برای اندازهگیری نیروهای چسبندگی/چسبندگی روی نمونههای آماده شده خاص استفاده میشود. آزمایشهای چسبندگی ساده بله/خیر با کشیدن دانههای مادهای که روی زیرلایههای مورد نظر خشک شدهاند، انجام میشود.
دستگاه اندازهگیری سختی Shore-A سختی لاستیک را اندازهگیری میکند. این دستگاه شبیه یک وزنه و یک گیج است که نوک آن به نمونهی عملآوریشده فشار میآورد. هرچه نوک بیشتر در لاستیک نفوذ کند، لاستیک نرمتر و مقدار آن کمتر میشود. سختی یک درزگیر ساختمانی معمولی در محدودهی ۱۵ تا ۳۵ خواهد بود.
زمانهای پوست در طول زمان، زمانهای بدون چسب و سایر اندازهگیریهای ویژه پوست یا با انگشت یا با ورقهای پلاستیکی دارای وزنه انجام میشود. زمان قبل از اینکه پلاستیک بتواند به طور تمیز جدا شود، اندازهگیری میشود.
برای افزایش طول عمر مفید، لولههای درزگیر یا در دمای اتاق (که به طور طبیعی ۱ سال طول میکشد تا یک سال طول عمر مفیدشان ثابت شود) یا در دماهای بالا، معمولاً ۵۰ درجه سانتیگراد به مدت ۱، ۳، ۵، ۷ هفته و غیره، پیر میشوند. پس از فرآیند پیرسازی (در حالت تسریعشده، به لوله اجازه خنک شدن داده میشود)، مواد از لوله اکسترود شده و به صورت ورق کشیده میشوند تا در آنجا پخته شوند. خواص فیزیکی لاستیک تشکیل شده در این ورقها مانند قبل آزمایش میشوند. سپس این خواص با خواص مواد تازه ترکیب شده مقایسه میشوند تا طول عمر مفید مناسب تعیین شود.
توضیحات دقیق و جزئی اکثر آزمایشهای مورد نیاز را میتوان در کتابچه راهنمای ASTM یافت.
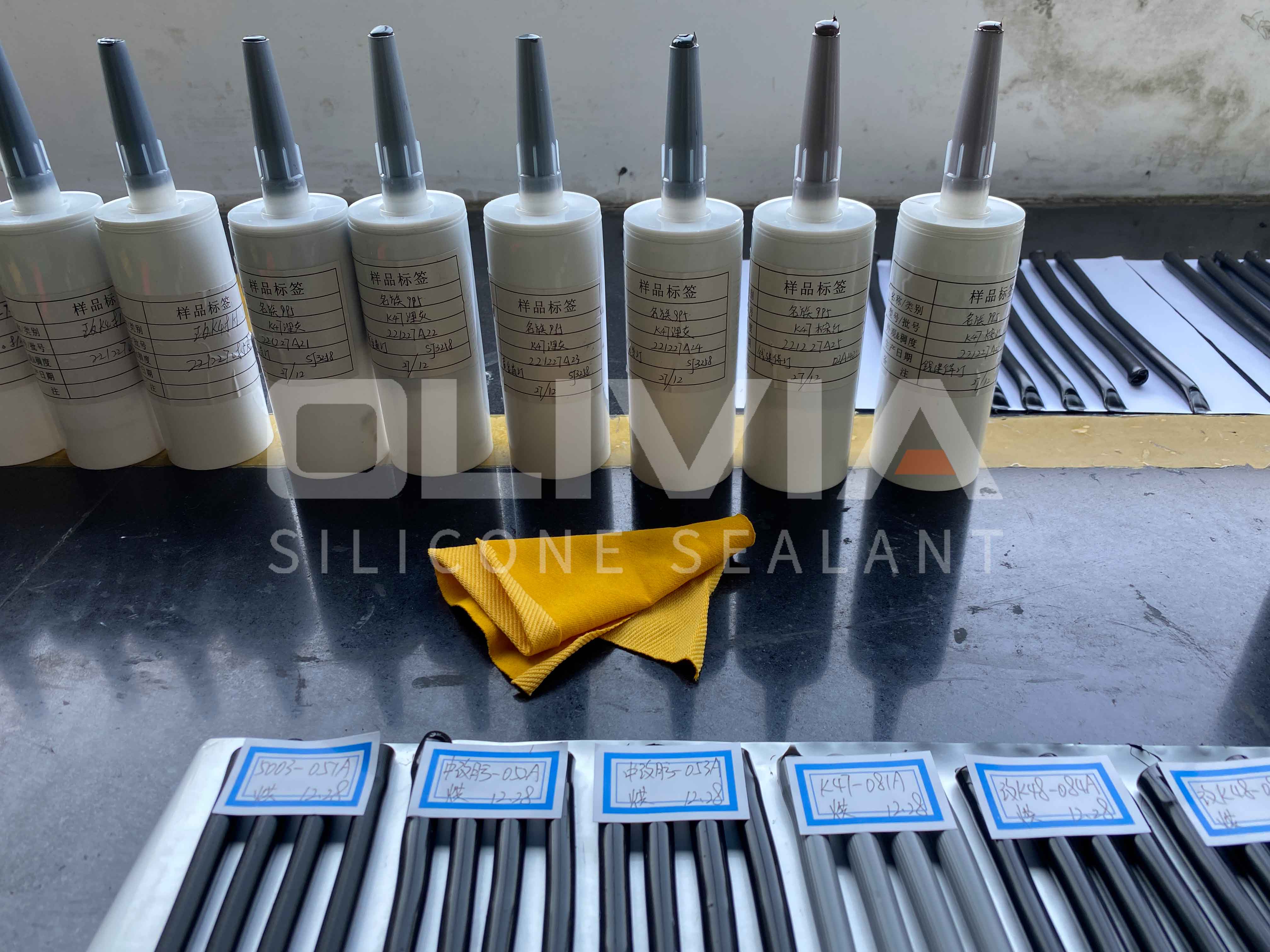
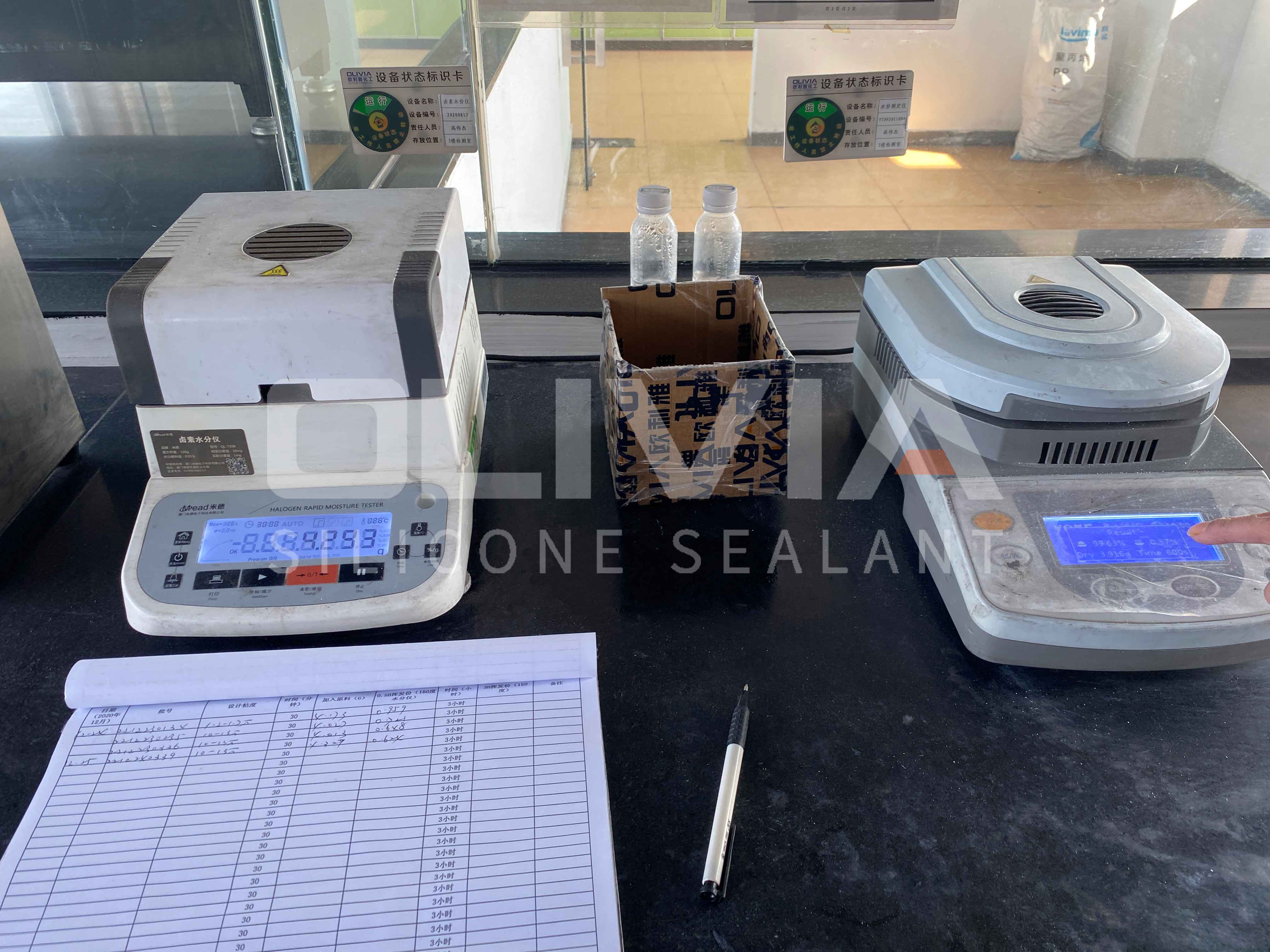
چند نکته نهایی
سیلیکونهای تک جزئی، باکیفیتترین درزگیرهای موجود هستند. آنها محدودیتهایی دارند و در صورت نیاز به الزامات خاص، ممکن است بهطور ویژه توسعه داده شوند.
بسیار مهم است که مطمئن شوید تمام مواد اولیه تا حد امکان خشک هستند، فرمولاسیون پایدار است و هوا در فرآیند تولید حذف میشود.
توسعه و آزمایش اساساً برای هر درزگیر تک جزئی صرف نظر از نوع آن، فرآیند یکسانی دارد - فقط قبل از شروع تولید در مقادیر زیاد، مطمئن شوید که تمام ویژگیهای ممکن را بررسی کردهاید و درک روشنی از نیازهای کاربرد دارید.
بسته به الزامات کاربرد، میتوان شیمی پخت صحیح را انتخاب کرد. به عنوان مثال، اگر سیلیکون انتخاب شود و بو، خوردگی و چسبندگی مهم تلقی نشوند اما هزینه کم مورد نیاز باشد، استوکسی انتخاب مناسبی است. با این حال، اگر قطعات فلزی که ممکن است خورده شوند درگیر باشند یا چسبندگی ویژه به پلاستیک با رنگ براق منحصر به فرد مورد نیاز باشد، به اکسیم نیاز دارید.
[1] دیل فلکت. ترکیبات سیلیکون: سیلانها و سیلیکونها [M]. Gelest Inc: 433-439
* عکس از درزگیر سیلیکونی OLIVIA
زمان ارسال: ۳۱ مارس ۲۰۲۴